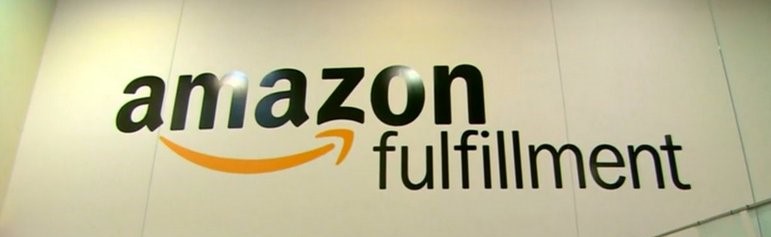
15 mrt Lessen uit het Fulfilmentcenter van Amazon
Wat ik leerde bij Amazon in het Fulfilmentcenter
Nieuwsgierig als ik was, stond ik om 11 uur met een groep van 10 logistiek professionals te popelen voor de poort van het fulfilmentcenter van Amazon in Koblenz voor een rondleiding. Het bedrijf is trendsetter met logistieke innovaties als pickrobots, experimentele drones en een eigen wereldwijd transportnetwerk. Wat kon ik verwachten? Ik trof een geoliede machine, ontdekte enkele onorthodoxe elementen en vond een aantal lessons learned.
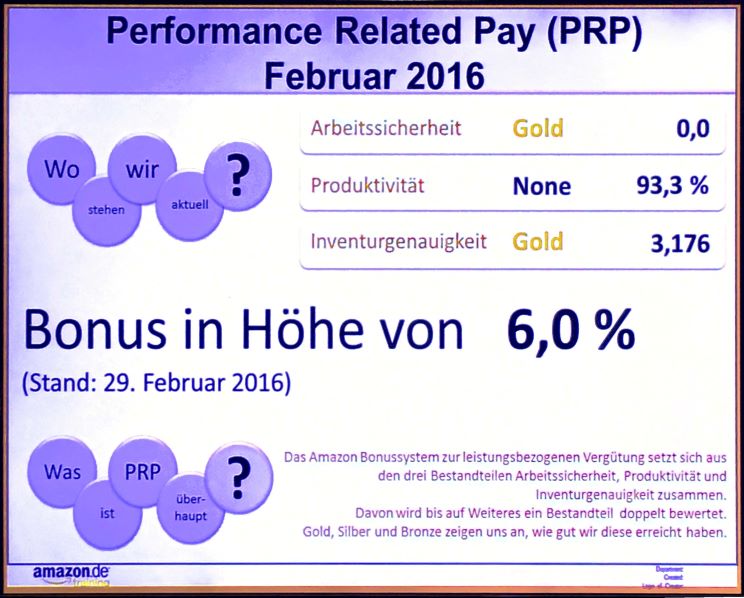
Ingang van fulfilmentcenter Koblenz.
Prestatiebeloning op veiligheid, productiviteit en voorraadbetrouwbaarheid.
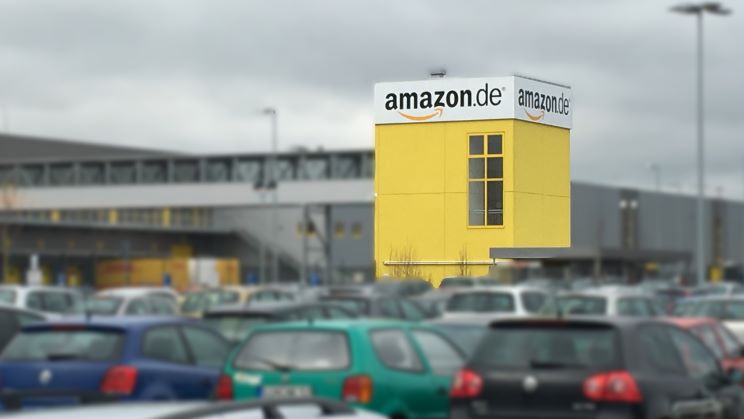
We gingen door een draaihek naar binnen en liepen via de gele toren en lange slurf het 110 duizend vierkante meter grote gebouw binnen. In de ontvangsthal hing een monitor met de laatste KPI-scores. De medewerkers van CGN1, Amazon vernoemt fulfilmentcentra wereldwijd naar de dichtstbijzijnde vliegvelden, hadden in februari een prestatiebonus van 6% verdiend.
20 vrachtwagens
Van de ontvangsthal liepen we het fulfilmentcenter in, richting goederenontvangst. Het was opvallend rustig. Ondanks de enorme schaalgrootte komen er slechts 20 vrachtwagens per dag binnen, in de piek oplopend tot circa 40. Binnenkomende zendingen worden echter wel vooraf geconsolideerd tot volle vrachten door logistiek dienstverleners. Op het terrein zie je zodoende veel gele opleggers en wisselbakken met DHL opdruk staan.
Eindejaarpiek
In totaal werken er 1.500 medewerkers in het fulfilmentcenter. Daar mag je in de eindejaarspiek nog zo’n 1.000 man bij optellen. Amazon zegt mensen aan te nemen ongeacht leeftijd of opleiding. Onze gids Andreas, een man in de zestig en vanaf de tweede maand werkzaam in het fulfilmentcenter, vond dat een mooie kans. De sfeer op de werkvloer leek me goed. Men was vriendelijk en enthousiast en wilde me graag verder helpen. Het kwam niet over als de sweat shop die soms in de media geschetst wordt waarin iedere medewerker tot het uiterste wordt gepusht.
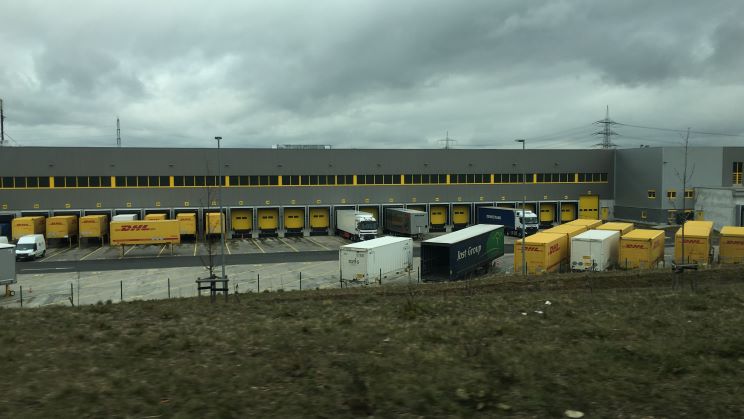
Geen bulkvoorraad
Grote producten op pallets gaan van de goederenontvangsthal rechtstreeks naar één van de vier hallen met pickvloeren. Dat is gelijk het eerste opmerkelijke principe van dit immense fulfilmentcenter: er is geen bulkvoorraad! Alle voorraad staat op picklocaties.
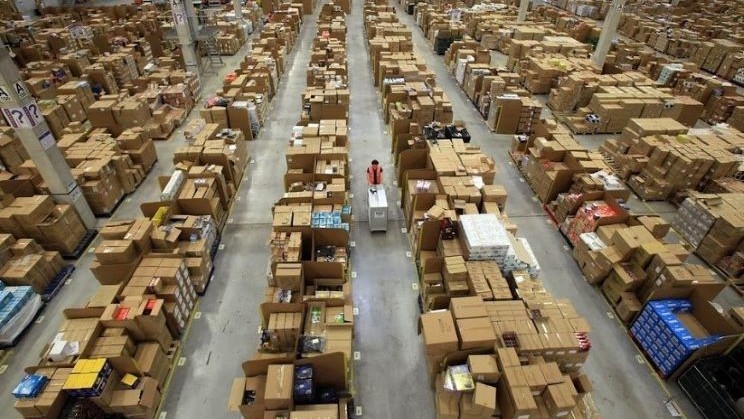
Pickvloer met pallets (Foto Business Insider).
Barcodenummer
Kleine producten worden ontvangen op ontvangststations. Binnenkomende dozen bevatten overigens geen documenten. Toeleveranciers dienen inkoopordernummers in barcode op verzendlabels te vermelden en de doosinhoud digitaal naar Amazon te sturen. De ontvangstmedewerker scant het barcodenummer en het WMS van Amazon weet welke producten het kan verwachten. De medewerker scant vervolgens de losse producten die uit de doos komen en legt ze in gele bakken. Er gaan verschillende producten in een bak en zodra deze vol is duwt de medewerker hem op een transportband. Als er orders openstaan voor het artikel, dan geeft het systeem een melding en legt de medewerker de stuks in een lege bak die direct naar een cross-dockzone vertrekt. Mocht er iets mis zijn met een ontvangst, dan gaat de gele lamp boven het ontvangststation branden. De medewerker gaat verder met het volgende artikel, terwijl een problem-solver het probleem voor zijn rekening neemt. Ook is er een rode lamp voor acute gevallen.
Cubiscan
Producten die voor de eerste keer binnenkomen worden naar een speciaal station gebracht waar gewicht en dimensies gemeten worden op een Cubiscan-apparaat. De uitkomsten worden wereldwijd gedeeld met alle fulfilmentcentra. Amazon heeft de maten en gewichten blijkbaar goed onder controle want het station stond er tijdens ons bezoek verlaten bij.
Picktoren
De transportband brengt de gele bakken van het ontvangststation naar één van de vier verdiepingen van de picktoren. Daar verdeelt een medewerker de inhoud naar eigen inzicht over legbordlocaties. De handscanners geven geen sturing. Amazon noemt dit chaotische opslag. Een principe dat ze al sinds 2005 hanteren. Een artikel kan derhalve op meerdere plekken liggen. Om de vulgraad van de legborden toch op peil te houden, mogen verschillende artikelen in hetzelfde vak gelegd worden.
Verdiepingen met legborden in de picktoren (Foto Business Insider).
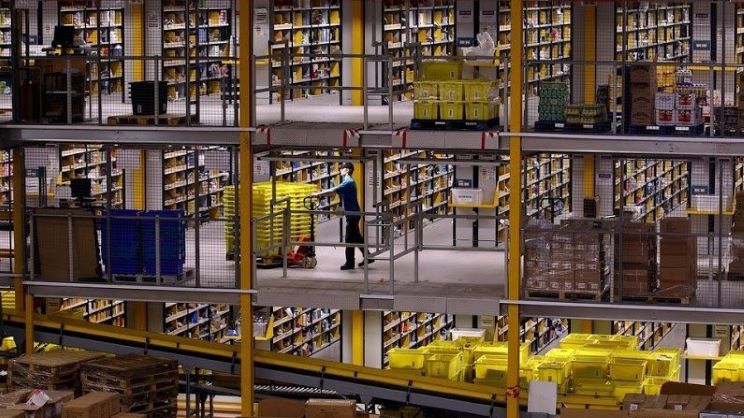
Transshipments
Amazon heeft 9 fulfilmentcentra in Duitsland. Niet ieder artikel ligt echter in ieder fulfilmentcenter. Zo gebeurt de printing on demand van boeken bijvoorbeeld alleen in Leipzig. De systemen van Amazon kijken bij iedere klantbestelling uit welke vestiging het best geleverd kan worden en nemen daarbij de workload en voorraadbeschikbaarheid in overweging. Als de producten voor een bestelling uit meerdere vestigingen komen, dan maken de systemen de afweging om afzonderlijke pakketjes naar de klant te sturen of de producten samen te voegen. De resulterende zendingen tussen fulfilmentcentra noemt Amazon transshipments. Deze komen in zwarte bakken het fulfilmentcenter binnen om vervolgens in een speciaal pickgebied opgeslagen te worden.
Amnesty
Order-pickers lopen met karretjes rond en verzamelen producten in gele bakken voor meerdere bestellingen tegelijk. Per pickronde verzamelen ze een batch van zo’n 50 artikelen uit de legborden. Single-piece en multi-piece orders worden in aparte rondes verzameld. De handscanners vermelden bij iedere pick hoelang ze erover mogen doen. Als pickers klaar zijn met een pickronde, dan zetten ze de bakken op een transportband. Mochten ze onderweg artikelen tegenkomen die beschadigd zijn, dan leggen ze die in een damage-locatie. Artikelen die los rondslingeren, leggen ze in de amnesty-locatie. De problem-solver lost het vervolgens op, zodat de pickers altijd verder kunnen met hun werk.
Order-pickers verzamelen bestelde producten in gele bakken (Foto Wimp.com).
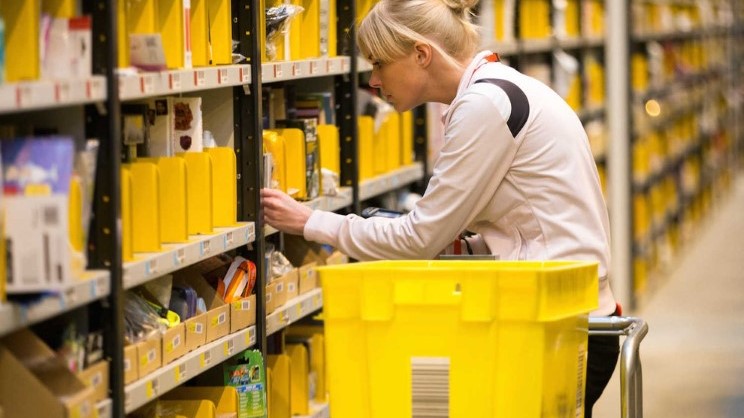
Robots
In de Duitse fulfilmentcentra van Amazon rijden nog geen robots. Amazon heeft de oranje Kiva-robots, vanwege de bedrijfsovername door Amazon in 2012 omgedoopt tot Amazon Robotics, in 2015 voor het eerst in Europa ingevoerd in een nieuwe vestiging in Wrocław in Polen.
Amazon robotics (Foto Newsweek)
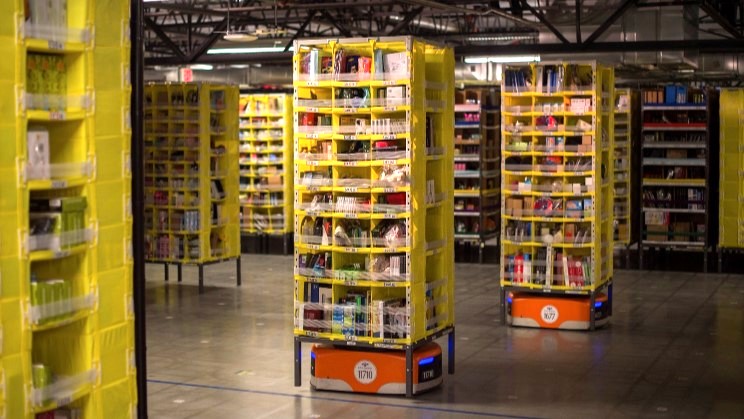
Wrangling
De gele bakken met single-piece orders gaan via de transportband rechtstreeks naar inpakstations. Bakken met multi’s, afkomstig uit diverse zones, komen samen bij een zogenaamd wrangling station. Hier sorteren medewerkers met de hand de bakken per batch. Gezien de immense schaalgrootte van het fulfilmentcenter is dit een buitengewoon kleine en simpele operatie. Doorgaans zie je flinke tussenbuffers en sorteerinstallaties in magazijnen om goederen uit verschillende zones samen te voegen. Het lukt Amazon echter om de voortgang in de diverse zones nauwgezet te synchroniseren, waardoor een batch in iedere zone ongeveer tegelijk klaar is. Om dit te realiseren, moet het zelfgebouwde WMS van Amazon over een intelligente besturing beschikken. De kern van de besturing zit enerzijds in de normtijden per pick die order-pickers op hun RF-schermen zien. Anderzijds speelt de chaotische opslag een belangrijke rol. Doordat producten op meerdere plekken liggen, kan het WMS de picklocaties zo kiezen dat de werklast evenredig over de zones verspreid wordt.
Re-bin station
Van het wrangling station gaan de gele bakken per batch op een kar naar het re-bin station. Hier worden de artikelen in de batch gesorteerd in een mobiele kast met een vakje per klantbestelling. Als de batch gesorteerd is, gaat de kast naar een inpakstation. Hier worden de klantbestellingen ingepakt, de medewerker sluit de doos en plakt er een kleine barcodesticker op. Evenals bij ontvangst, zitten er geen documenten in. De dozen vertrekken op een transportband naar het expeditiegebied. Onderweg wordt de doos automatisch van het juiste verzendlabel voorzien. Aan het eind van de band leggen medewerkers de pakketjes in rolcontainers. De rolcontainers vertrekken tenslotte in vrachtwagens.
Seizoenspieken
Het is duidelijk tijdens de rondleiding dat Amazon met seizoenspieken te kampen heeft. Zo staat er een hele hal leeg in afwachting op de eindejaarspiek. Om dezelfde reden zijn hele straten met inpakstations bedekt onder afdekzeilen.
Lessons learned
Wat viel het meeste op en wat kunnen eCommerce-bedrijven leren van Amazon?
-
- Het proces is geheel papierloos.
Absoluut een best practice en een duidelijke trend, denk maar aan de initiatieven rond papierloos transport. Toch zijn nog veel bedrijven hier niet aan toe. - Er is geen bulkvoorraad.
Veel bedrijven zien hun fulfilmentcenter als opslagmagazijn, terwijl ze het wellicht beter als winkel zouden kunnen beschouwen. Ik zou niet willen zeggen dat bulkvoorraad in fulfilmentcentra een bad practice is, maar probeer het beperken tot producten waarvan meer dan een pallet per week de deur uitgaat. - Producten worden chaotisch opgeslagen.
Doorgaans wordt dit principe als bad practice beschouwd vanwege toenemende zoektijd, minder compacte opslag en grotere foutkans. Toch heeft Amazon hier een goed werkende variant op bedacht. Ik ben benieuwd welke bedrijven het voorbeeld van Amazon zullen volgen. - Pickprocessen lopen synchroon.
Door order-pickers volgens normtijden te laten werken en oponthoud te elimineren, wordt de voortgang voorspelbaar en planbaar. Slimme algoritmes in het zelfgebouwde WMS zorgen er vervolgens voor dat de voortgang in alle zones gelijktijdig verloopt waardoor het samenvoegen van bestellingen eenvoudig wordt. Dergelijke intelligentie heb ik niet eerder in WMS-pakketten gezien. Een mooie uitdaging voor WMS-leveranciers lijkt me. - Voorraden worden gedeeld
De longtail speelt een belangrijke rol bij Amazon. Het is echter kostbaar om ieder product overal op voorraad te leggen. Om desondanks nee-verkoop te voorkomen, delen de fulfilmentcentra onderling voorraden. Nu beschikt niet ieder bedrijf over 9 fulfilmentcentra, zoals Amazon in Duitsland. Toch hebben andere bedrijven wellicht mogelijkheden om ontbrekende voorraad te leveren vanuit winkels of rechtstreeks van leveranciers.
- Het proces is geheel papierloos.
Naschrift: Binnen de muren van het fulfilmentcenter was fotograferen niet toegestaan. Derhalve heb ik foto’s van andere bronnen gebruikt. Deze foto’s zijn genomen in andere fulfilmentcentra van Amazon, maar lijken sterk op hetgeen we in Koblenz zagen.
Sorry, het is niet mogelijk om te reageren.