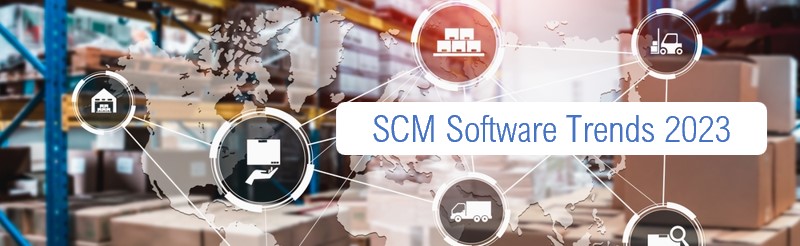
03 May Survey SCM Software Trends 2023
Companies want more grip on their supply chain
Companies have reached the limits of their business systems. After the turbulent start of the decade, it has become clear that they have insufficient control over their supply chains. Now they are looking for software that allows their supply chains to operate as a coherent whole, resulting in a significant shift towards specialized best-of-breed packages.
This is the main conclusion of the SCM Software Trends Survey 2023 by Jeroen van den Berg Consulting. We investigated twenty recent supply chain software projects of companies in various markets from the manufacturing industry to e-commerce. Enterprises purchase new supply chain software to get more grip on their supply chains. Many lost control in recent years due to global materials scarcity and extreme demand fluctuations as a result of corona and the Ukraine war. Other motives for investing are cost savings, growth, the introduction of new services and compliance with laws and regulations.
Shortcomings
Companies indicate that they are reaching the limits of their business software. Their main shortcomings are:
- Inadequate support of business processes
- General lack of information
- Information inconsistency between departments
- Systems are hard to adapt
In addition, in some cases replacement is necessary because vendors no longer support the software.
These shortcomings demand substantial efforts in the day-to-day business operations. All kinds of stand-alone tools and handy excel spreadsheets are being created to be able to get the goods out. As a result of this island automation, not everyone in the company views the same information. Subsequently, departments need to deal with eachother intensively outside of systems. This typically happens at the last minute, which results in a lot of stress and hassle. Or it is completely forgotten with all its associated consequences. Just think of the classic rush order that ends up at the back of the queue in the warehouse.
IT landscape overhaul
Although our research initially focused on companies that were looking for a new warehouse management system (WMS), it was immediately clear that many of them needed more. No less than 40 percent renew their entire IT landscape, including ERP and other systems. That is where the puzzle begins. Which puzzle pieces in the IT landscape should be replaced and which may stay? How to make it all fit again? What is the best roll-out sequence? And how to ensure that it continues to work in the meantime? Many complex questions!
Best-of-breed popular
What can we learn from the case studies? Traditionally, there have been two options for automating business processes: a company-wide ERP or a best-of-breed architecture with specialist packages and interconnections. In the survey we see a significant shift to best-of-breed. Although 70 percent of the cases initially use a company-wide ERP with integrated WMS, that only holds for 20 percent afterwards. There is even one wholesaler that opts for an architecture without ERP. They chose a central e-commerce platform supplemented with specialist cloud packages.
Many of the companies believe that specialist packages support their business processes better than generic ERP systems. Moreover, linking business systems has become easier thanks to modern techniques such as web services. Finally, they believe that the risk of introducing the new software all at once is too high. They prefer the step-by-step replacement of smaller systems.
Big bang too risky
How do companies replace their business software? The transition to the new IT landscape requires a well-considered approach. Only ten percent of the considered cases opt for a big bang in which all systems are replaced by new software at once. The advantage of this approach is that no intermediate solutions are required. However, most companies find such a rigorous step irresponsible.
The most popular approach is to peel off the ERP, layer-by-layer, like an onion. By constantly transferring functions from the old ERP to new systems, it gets smaller and smaller. Think of new systems such as PIM (products), CRM (customers), HRM (personnel), BI (management information), MES (production), TMS (transport) and WMS (warehousing). What remains is the core of the ERP with production planning, inventory management, order management and finance. This makes it manageable to eventually replace the ERP as well.
End-to-end supply chain
The survey reveals that companies today look at business systems in a different way. Supply chains have become more and more unpredictable. The trend is that companies seek integrated support for their end-to-end (E2E) supply chain from purchasing and production to customer delivery and after-sales.
They believe that current software focuses too much on individual departments. Business processes must be integrated and systems should connect seamlessly. In this way they can better deal with supply chain disruptions. At the same time, companies seek opportunities for improvements in customer service, efficiency, scalability and regulatory compliance. The composition of the future IT landscape and the roll-out plan are still a puzzle for many. Nonetheless, best practices seem to be emerging. More about this in part two of this series on our SCM Software Trend Survey 2023.
Sorry, the comment form is closed at this time.