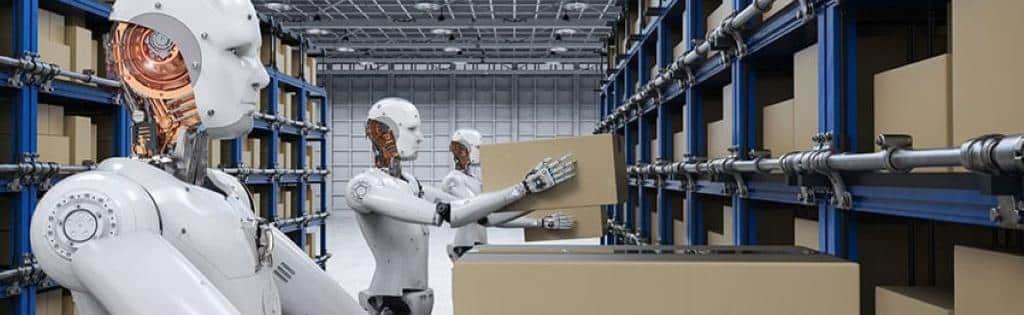
23 Sep Trends in warehousing 2024
We live in turbulent times, also in logistics. Companies feel that they are losing control over their supply chains. What challenges do logistics managers face and which choices do they make? What does this mean for warehouses? Here are the 5 most important trends in warehousing for 2024.
Logistical challenges
In 2023, I analysed twenty projects of companies looking for new WMS packages for their warehouses. The greatest common factor in these cases was the need for control over the supply chain. Last year was an extremely uncertain moment in time, just a year after the corona pandemic and the outbreak of the war in Ukraine. Supply chains were volatile with faltering supply, instable prices and fluctuating demand. Companies had lost control over their supply chains. As a natural response, they looked for guidance in new systems that could provide more grip.
But companies also had other reasons to look for new logistics software. Companies with growth ambitions wanted to scale up their logistics operations, while others saw opportunities to expand their portfolios with new services. However, existing business systems were not equipped for their ambitions. In addition, staff shortages played tricks on many companies, resulting in stress and faltering deliveries. They also felt the pressure of laws and regulations on sustainability, food, customs, hazardous substances or safeguarding their own quality standards.
In short, companies were at their wits’ end. Continuing with current systems meant a liability to the continuity of the company. Nonetheless, many management teams demanded that the investments should pay for themselves through cost savings. In general, this was possible by eliminating inefficiencies from the supply chain.
Main logistical challenges:
-
- Volatile supply chains
- Staff shortages
- Business growth
- New services
- Laws and regulations
- Cost savings
Limits are reached
Companies saw that they reached the limits of their business software. Systems did not provide adequate support. Various companies were still using paper pick slips and office staff kept track of excel sheets to manage data that was missing from systems. There was a lot of siloed automation where business systems were not linked and little information was exchanged between departments. Moreover, it was complex to adapt the business software to new requirements, often due to large amounts of customization. In some cases, the vendor had even pulled the plug and announced that the software was end-of-life.
Trends in Warehousing
It is interesting to see which choices companies made to tackle their logistic challenges. In other words, what are the main trends in warehousing for 2024:
-
- End-to-end supply chain
- Digitalisation
- Robotisation
- Cloud
- Back to basics
1. End-to-end supply chain
In turbulent times, companies experience many disruptions which they cannot influence themselves. However, there are also disturbances that are within their circle of influence. It is important to get a grip on those. One wants to prevent things from going wrong due to employee mistakes or poor collaboration between departments. Take the classic example where Purchasing makes a big effort to get items delivered quickly and then they stay at the arrival hall of the warehouse for a week. Companies want to get rid of these disconnected links in supply chains. The first trend is that companies aim to create end-to-end supply chains. Supply chains in which information is shared and processes seamlessly connect for a perfect service to customers.
Serving the customer in the best possible way is key to the end-to-end supply chain. Companies want to be able to make realistic promises to customers. They want to know upfront if there is enough stock and how much time it takes to deliver to the customer. Additional services requested by customers are explicitly recorded.
In the past, promises to customers often disappeared into note fields in orders and were followed up with phone calls and post-it notes. That is different in the end-to-end supply chain. Agreements are explicitly recorded in systems and automatically shared and followed up. For example, if a customer is promised that a metal pipe is shortened by 1 metre, then warehouse workers are automatically instructed to take the pipe past the sawmill before it leaves the premises.
In addition to new systems, the end-to-end supply chain also requires different ways of collaboration between departments. Many disruptions occur between departments. For example, a sales person promises at the end of the afternoon that the order will be shipped today. Such last minute actions cause a lot of hassle and stress. In the end-to-end supply chain, departments make formal agreements about services and delivery times. In this way, they prevent excesses and processes are more manageable and plannable. If urgent shipments are essential for the company, then this is arranged in the formal agreements, for example that a maximum of 5 urgent shipments per day are allowed.
2. Digitalisation
The second trend is digitalisation of warehouse processes. No more paper lists in warehouses and no more loose excel sheets. The premise of digitalisation is that there is only one truth. So one stock level, one delivery date, one priority and the information may not differ between systems. This is called single source of truth. One system acts as source and shares its information with other systems. Information is up-to-date, accurate, unambiguous and accessible to those who need it.
At the same time, digitalisation ensures efficient, flexible and scalable processes. Efficiency through smart controls and the elimination of unnecessary process steps. Flexibility through systems that can easily be adjusted via business rules, preferably by your own people. Scalability by accommodating the necessary knowledge in systems. As a result, you no longer depend on people’s knowledge and experience and you can train new employees more easily. In addition, decisions can be automated so that you no longer depend on the work of people in back offices.
Even in new systems, it remains essential to avoid customization. So design a streamlined warehouse operation with as few exceptions as possible. The primary warehouse process “inbound-storage-outbound” must run smoothly. Special services for customers should not interfere with this process. Therefore, we can introduce separate work stations in the inbound and outbound flows. At these work stations, operators can perform value-added services such as labelling, auditing, repacking, bundling or whatever else is required. The WMS automatically routes all exceptions through these stations, so that standard processes are not disrupted.
Finally, digitalisation must ensure that processes are carried out in accordance with laws and regulations. Think of legislation in the field of food safety, sustainability, customs, fire safety, dangerous goods or ensuring your own business objectives for sustainability or product quality. Systems ensure that the work is carried out in accordance with the rules and record executed work tasks for tracking and tracing, so that any discrepancies can be traced.
3. Robotisation
The third trend is robotisation and mechanisation in warehouses. In recent years, we have seen enormous developments in this field. Material handling suppliers have designed new systems that deliver goods to order pickers efficiently and in high volumes. Popular systems such as Autostore, shuttles and picking robots enable automated picking of pallets, boxes or individual pieces. There are also mechanized solutions for transporting, sorting, packing, and consolidating goods in warehouses.
A point of attention is the control of the mechanization and robots. Automated material handling systems have their own control software. Their so-called warehouse control system (WCS) receives tasks from the WMS and ensures that robots, cranes and sorters carry them out properly. The software is usually less easily customised than a WMS. If several automated systems are running side by side, each with its own WCS, the WMS distributes the work among the systems and sends tasks to each WCS separately. This works fine if the systems operate separately from each other. However, if there is mutual interaction between systems, then it becomes harder. A new development concerns warehouse execution systems. These are systems that are easier to adapt and enable complex control across multiple systems.
4. Cloud
The fourth trend is software in the cloud. There are WMS packages that have been around for 20-30 years. These packages are rich of functionality, but no longer meet the latest technological standards, user-friendliness leaves much to be desired and it is hard to make changes. We see that vendors of these packages are either developing new packages from scratch or revising their existing packages with cloud being the new standard.
Modern WMS packages are easy to link to other systems via APIs. There is also a lot of freedom in configuring processes and controls via business rules. In fact, all information available in a system can be used in control logic, so that you are not restricted to a few pre-defined options. Finally, packages are regularly updated to new versions so that the software no longer becomes obsolete.
5. Back to basics
Then we come to the final trend. It is not artificial intelligence, as you might expect. There is no denying that developments in AI are moving at lightning speed with applications in more and more domains. However, in logistics software, we do not yet see much of generative AI and machine learning. For the time being, “AI” is restricted to traditional algorithms and calculation rules.
The fifth trend that we observed was a back to basics movement. Companies are taking a critical look at their business operations and rationalizing their services. Over the past decade, we have seen companies offer faster and more comprehensive services, often for free. Typically with the aim to grow quickly and grab market share. Now we see that companies reach their limits and scale back their services. For example, Wehkamp.nl recently started charging for returns or the flash delivery services like Getir, Gorillas and Flink that disappeared as quickly as they came. Another striking example was a wholesaler who shortened its cut-off time from 5 PM to 2 PM for next-day delivery. As a result, it was no longer necessary to work evening shifts. This made it easier to recruit staff. Furthermore, the workload was better distributed throughout the day with less idle time in the morning. It increased complete deliveries and lowered costs. More companies will rationalise their services under the pressure of staff shortages, environmental impact or cost considerations.
Conclusion
The past few years have been hectic and unpredictable. Companies wanted more grip on their supply chains. Control, flexibility and scalability were paramount when choosing new logistics software. Modern systems provide insight and ensure seamless collaboration. Developments in robotics and cloud software make it easier to automate warehouse processes. At the same time, take a critical look at your own services, do you need to do better or should you perhaps do a little less?
Sorry, the comment form is closed at this time.