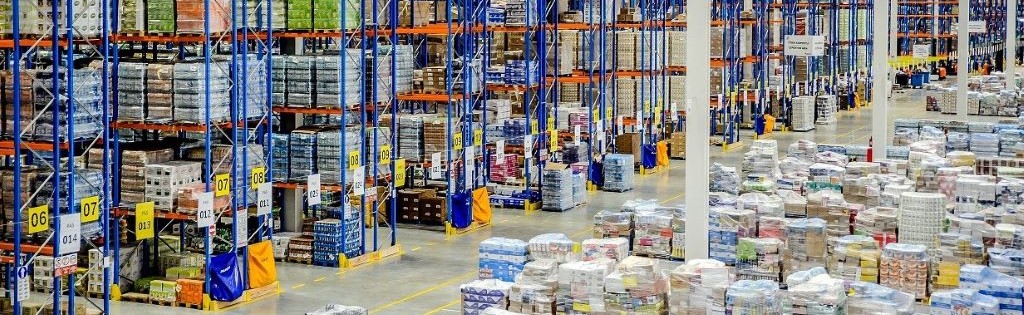
14 Jan Silent revolution in warehousing
Silent revolution in warehousing
Digitalization, market places, e-commerce, omnichannel, drop-shipping: the way we do business has revolutionized in recent years. However, things seem to remain the same within the four walls of the warehouse. Yet a silent revolution is currently taking place there.
Nowadays it is literally more of the same in warehouses: wider assortments, higher stock turnover rates, more volatile demand patterns and faster more finely meshed deliveries. Traditional logistics solutions reach their limits. New solutions are needed. In the shadow of the digital transformation, a silent revolution is taking place in warehouses.
The previous revolution in warehousing occurred in the years prior to the turn of the millennium. Warehouses became paperless. The work of order pickers changed dramatically. They no longer carried paper pick slips, but received their tasks directly from the warehouse management system (WMS) via wireless terminals or, later, via voice headsets. The WMS directed and controlled all activities in real-time. The result was more efficiency and fewer errors.
We are now 20 years further and the real-time systems are reaching their limits. A few extreme orders, an urgent delivery in-between, a returned pallet or a busy day, they used to be manageable exceptions. That time is over. Warehouses nowadays serve multiple sales channels with varying order patterns and extreme demand peaks while urgency is the norm. The exception has become the rule.
Top 5 innovations
How do warehouses deal with the increased complexity, volatility and time pressure? Technical innovations offer solutions. Autostores, vertical lift modules, shuttle systems, pick robots, packing machines, all kinds of high-performance material handling systems that relieve operators of part of their work. However, with or without these systems, today’s logistics operations require more cleverness. In this article I discuss the top 5 innovations in WMS.
-
- Fulfilment
- Waveless picking
- Volumetrics
- Transport integration
- Workload planning
1. Fulfilment
Fulfillment refers to today’s fine-meshed logistics, mostly for web shops. By cleverly combining tasks and rationalizing procedures, this type of logistics can also be carried out efficiently. Here is a list of fulfillment variants on common procedures that are supported by modern WMS packages:
- Multi-order pick: Order pickers have carts with multiple bins and sort items per order during their picking rounds to the correct bins.
- Single-piece pick: Single-piece orders only consist of 1 piece. Operators pick pieces for multiple orders at once and take them directly to the packing table where they are packed one by one.
- Packing: Efficient support for packing orders into shipping cartons, including checking of contents, selecting carton sizes, carriers and shipping methods, printing documents and shipping labels and automatic pre-advice to carriers.
- Chaotic storage: Put different items at the same pick location to save space. Order pickers scan barcodes on items to prevent picking errors.
- Cross-dock: E-commerce is characterized by a long tail of slow-moving items that are not necessarily in stock. Such items are purchased as soon as there is demand. Can the item be delivered directly to the customer after receipt? Does it have to be merged with inventory from the warehouse? Or does it need to wait until all stock for the customer order is available? Depending on the situation, there are different ways of cross-docking.
- Returns: E-commerce has many returns. The receipt process for returns is similar to regular goods receipt, but there are differences. For example, operators must determine whether return conditions are met and whether items are still in good condition. The WMS should dig up the relevant information.
Multi-order pick: order-pickers put items directly into the right cartons.
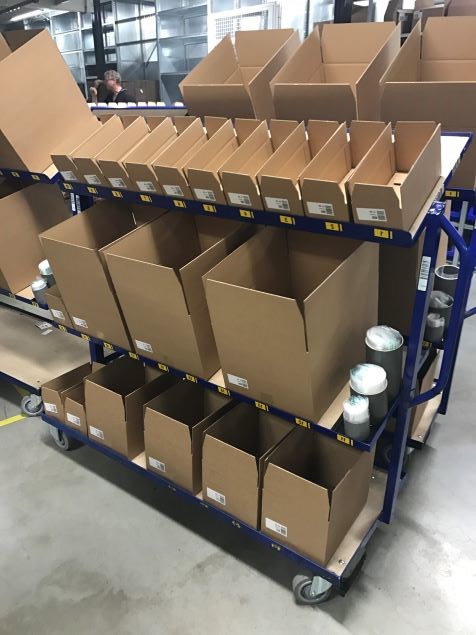
2. Waveless picking
The increased speed of delivery is another challenge. Traditionally, response times were A-for-C. On day A, orders arrived, on day B they were picked to arrive at the customer on day C. In the morning, we knew exactly which orders we needed to pick in the warehouse that day. In addition, all outgoing transports were already planned in advance so that, after picking, orders could be placed directly on the right lane for loading into the truck. During the day, orders were released for order picking per wave in the WMS. Such a wave was a set of orders with similar departure times. The WMS did extensive calculations for each wave to put together efficient picking tasks.
In the meantime, response times have been shortened to next day or even same day delivery. Incoming orders must be picked on the same day. This makes working per wave far too static. With waveless picking, orders become immediately available for order pickers. As the order set is constantly changing, the WMS can no longer calculate everything in advance. Instead, there is intelligence in the WMS that considers the current situation and puts together picking tasks for operators at the last minute. An urgent order no longer needs to wait for the next wave. This allows warehouses to respond faster.
3. Volumetrics
It is important that orders are compactly packed to keep transport costs low, especially with the wide variety in order profiles of today. Traditionally, operators picked their orders on pallets until they were full. If the order was not yet complete, then they would continue on the next pallet. Preferably, one order picker collected the entire order. If multiple order pickers worked on the same order, then it would result in half-full pallets. It is quite a challenge to assemble these into compact truck loads.
A modern WMS calculates volumes per order in advance and puts together efficient picking rounds in which order pickers assemble full pallets or boxes. This saves walking meters since order pickers no longer have to traverse the entire warehouse for a single order. Moreover, it shortens lead times since multiple order pickers work on the same order simultaneously. Another advantage is that during order picking, products can be placed directly in the correct shipping container. That eliminates a lot of packing work.
To calculate the volumetrics, the WMS needs correct volume data for items. That is often a problem. With almost every WMS implementation nowadays, people do an inventory of weights and dimensions beforehand. Afterwards, all new items must also be measured. There are devices available on the market for this purpose that automatically determine sizes and weights.
4. Transport integration
In recent years, carriers have rolled out networks for efficient distribution of individual shipments. At night, they sort shipments at transfer hubs into full truck loads to deliver them to customers on the next day. The large volumes make it easier for carriers to create efficient trips than for individual warehouses.
Nevertheless, for warehouses with sufficient cargo for full truck loads, it is cheaper to have trucks depart from the warehouse directly to customers. However, if new orders arrive all day, then we cannot determine in advance which orders will go on which trip. Still, order pickers do get started and stage picked goods in a buffer. From the buffer, orders are consolidated into full truck loads as soon as the transportation planning is finalized. This requires close integration between the WMS, which calculates transport volumes in advance, and the transport management system (TMS) that schedules distribution trips and departure times.
5. Workload planning
Many warehouses rely on temporary workers and employees with flexible contracts to cope with demand fluctuations. A modern WMS can also help with this. On the one hand by making a calculation in advance of the workload for a day based on historical patterns and incidental events. On the other hand, by monitoring the progress during the day and make proposals for exchanging people between departments.
Traditionally, the focus of WMS packages was on the execution of the work, while planning features remained underexposed. In my book Highly Competitive Warehouse Management I present models for workload planning in which expected demand is converted into working hours via labor standard times . It is nice to see that various WMS providers have adopted these models. This trend is still in its infancy, but hopefully it will proceed.
Keep Struggling
In current times, the complexity, volatility and speed of supply chains have increased dramatically. Classic ways of working have reached their limits. In the shadow of the digital transformation, a silent revolution is currently taking place in warehouses. Innovations in planning, control and procedures help to break boundaries.
Has your warehouse also reached its limits? Check whether the top 5 innovations can help you forward. Could your current WMS provide adequate support or is it time for a new system? Savings typically are substantial compared to investments. Moreover, it helps your company to move ahead, because you can easily meet today’s market requirements.
Of course there is an alternative and that is to keep struggling….
Sorry, the comment form is closed at this time.